SofTech’s ProductCenter PLM Expedites the Worldwide Supply of Amway Products
ProductCenter PLM Improves Control of More Complex Engineering Data and Streamlines Product Processes
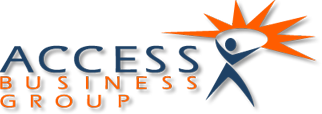
About Access Business Group:
Amway was one of the early pioneers of direct selling of laundry and home cleaning products. Over the decades, the Michigan-based Amway Corporation (now known as Alticor Inc.) has become well known not only for its products but also from the thousands of independent business owners who distribute them.
The Alticor family of companies consists of different business entities for the purpose of better handling the tasks of product development, production, and sales and distribution. Under the umbrella of the name Alticor, its subsidiaries Amway, Access Business Group, and Quixtar currently enjoy total worldwide sales of over $6 billion annually. The familiar Amway and Quixtar entities still sell, but Access Business Group supplies.
Access Business Group was formed to develop, manufacture, and distribute products for Alticor companies, as well as to develop and produce contract manufactured products. Due to this vast number of products, Access needed quick access to the thousands of documents they produced: designs, specifications, user manuals, and sales brochures.
The Situation:
“Our company produces more than soap. We produce an extensive line of market-leading water and air filtration systems, along with beauty, wellness, other home products, and contract manufactured products for other companies,” states Dennis Kool, Senior Group Leader of the Process and Engineering Support Group at Access. “Our engineering organization is always looking at new ways to apply technology or refine processes to enhance our product quality, reliability and customer satisfaction. This, coupled with increasing product diversity and complexity, led us on a search for a more comprehensive product data management solution.”
For years, Access Business Group had been utilizing a computerized text-based system for managing product data. The ‘green-screen’ was fine for managing chemical formulas for laundry soap products and the like, but as the company moved into durable products, such as water and air filtration systems, which now required engineering drawings, it needed a more appropriate method to manage increasingly more complex engineering data.
The Solution:
Access evaluated several proposed product data management/product lifecycle management (PDM/PLM) solutions.
“Our major concern was compatibility,” recalls Kool. “We wanted a solution that had proven experience with managing engineering and legacy data such as AutoCAD and Pro/ENGINEER files. We chose SofTech’s ProductCenter™ PLM solution on the strength of its integration to Pro/ENGINEER and its ability to accommodate other file types.”
Today, beyond vaulting and centralizing engineering data, ProductCenter assists Access in change-and-release management, and also functions as a helpful collaboration and communications tool throughout the company. “With ProductCenter, you can always be assured of working with the most current documentation. Productivity has increased. Engineering data in many forms is under centralized control and immediately accessible,” says Kool.
ProductCenter use has been expanded to non-engineering applications as well. For example, the Rapid Prototyping lab uses ProductCenter to store and control prototype .STL files, along with build-and-cost information for future reference and analysis. Similarly, Access’ worldwide Repair Service outlets view technical hotline flow charts and other support materials through ProductCenter. With ProductCenter’s security controls and Web-accessibility, the capability is in place to integrate outside design chain partners and suppliers.
The Future:
Next on the agenda at Access Business Group is further automation. For its design and review process of new products, Access can track changes through SofTech’s ProductCenter™ Workflow.
“I can create an engineering change order (ECO) form with the ProductCenter Forms Editor and then, with Workflow let users electronically route ECOs and data packages right from their design application,” says Kool. Reviewers can comment on changes and then sign-off using electronic signatures for approvals. “This will save more time and probably eliminate weekly review meetings,” he estimates. “By getting changes approved sooner, we can accelerate our manufacturing improvements for less cost.”
Another issue Kool is examining concerns bills of material (BOMs). Currently, a master BOM, or parts ticket as it is referred to at Access, is maintained in a separate document system to drive manufacturing, referencing associated product data stored in ProductCenter. This process works well for single level, formula-based BOMs, but with more complex product structures, Kool sees this area as ideal for further automation with the ProductCenter™ BOM Editor.
The ProductCenter BOM Editor allows for easy creation of more meaningful hierarchical BOMs, and through Reference Links will keep the BOM and other related product data, centralized and in-sync. Another timesaver is the capability to automatically populate BOMs from ProductCenter attributes to speed BOM creation, saving re-keying and ensuring data integrity between systems.
Access has now begun utilizing ProductCenter Workflow and the ProductCenter BOM Editor to initiate, route, review, and publish new service part BOMs into their document management system. Manufacturing assembly instructions are also being routed and reviewed electronically using Workflow.
“ProductCenter has helped us keep up with the evolving demands of our business,” said Kool. “Improved data accessibility and control has had a positive impact on engineering productivity.”