ProductCenter PLM Pure Success at Millipore
PLM Solution Facilitates Global Design and Manufacturing for Leading Industrial Purification Filter Manufacturer
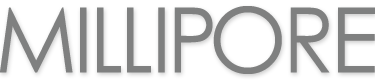
The Company:
Advertising agencies would lead you to believe the water used in beer production comes from clear mountain streams. But, if the truth be known, it’s not Mother Nature — it’s purification systems developed by Bedford, Massachusetts-based Millipore Corporation, a leading developer and manufacturer of purification filtration and related processing technologies.
In addition to food and beverage, Millipore is market leader in a number of other industries. Laboratories around the world use Millipore filter systems millions of times a day. In microelectronics manufacturing, Millipore purifies just about every gas and liquid used in creating a semiconductor device. In fact, Millipore products are used at 2,000 critical points throughout the process.
Millipore operates 15 global manufacturing facilities and employs over 4,800 people. The company’s mission is to achieve continued leadership, with a global focus on customer satisfaction, employee participation, and technical excellence. A critical element in supporting these objectives is from SofTech, ProductCenter™ PLM, a product lifecycle management (PLM) solution.
The Situation:
Globalization drove Millipore’s search for a product data management solution in 1994 and their selection of SofTech’s solution. “There was a need to exchange information across multiple time zones and country boundaries,” states Jim Donovan, Millipore product data management technology manager. “In those days, Millipore had a paper based system. When someone needed a print, they’d have to contact the owning facility to request a copy. With luck, it would show up a week or so later via pony express.”
Product development is done at Millipore design centers in Massachusetts, Japan, and France, and manufacturing at any one of the 15 facilities worldwide. Groups sometimes collaborate for product design and manufacturing is often shifted or shared between facilities. “Because of this, we needed documentation at the same revision level in three or more locations. I’m not sure we did it with 100% accuracy with the paper-based system.”
The Solution:
Millipore recently upgraded to ProductCenter from a much older version of the software. Donovan and his staff were challenged with upgrading four servers and a thousand desktops with the new software worldwide, without impacting operations. ProductCenter client software was sent out on a Wednesday. Servers were upgraded over the weekend and by Monday users were operational. The conversion was an overwhelming success.
“The first week we logged about 65 customer support calls – not a lot with 1,000 users really. Most of the calls were from employees who were not properly connecting to the network or had older versions of certain .dll files. A couple were questions on how to perform a function with the new version.” He adds, “We are exceptionally pleased with ProductCenter’s scalability performance. The new graphical user interface is impressive and easy to follow. Users were productive with just a half-an-hour of training. The feedback on the new version has been extremely upbeat.”
Asked what differentiates ProductCenter from other PLM solutions he’s seen Donovan replies, “SofTech’s ProductCenter’s breadth and quality of integrations, particularly their SolidWorks® and Pro/Engineer® integrations, is a significant competitive advantage for the company.”
Millipore standardized on Pro/Engineer early on and has recently seen a shift towards SolidWorks. “Over the years, SofTech’s solutions have earned extreme credibility with the design groups. It’s their core data management tool. Interestingly, much to my surprise, many of our engineers aren’t that concerned about what CAD tool they use, as long as the tool integrates with ProductCenter.”
One ProductCenter feature Millipore has been particularly pleased with is what Donovan terms its ‘bulletproof vault’. Each plant can access a list of documents they own, a requirement of ISO 9000 regulations, or access any document through ProductCenter, providing that they have permission. The information is instantly available, even with 1,000 users on the system and over 85,000 files stored in distributed vaults in three countries at four remote sites. Not once has Millipore experienced corrupted data. “We had one site that backed-up data to a local drive, then a group drive, and also put copies on floppy disks. After seeing ProductCenter’s reliability, they gained the confidence to give up all their redundant back-up processes.”
According to Donovan, ProductCenter has improved customer responsiveness, in particular on a recent customer audit of a Millipore manufacturing facility in Texas. “Our customer was ecstatic when they saw how well we controlled our plant level documentation with ProductCenter. Typically, audits lead to findings and then some clean up work.” He adds, “In this case, it was great to have a major customer want to bring in their people to look at our system. They thought ProductCenter was a world-class system.”
Early on, a few Millipore engineers were reluctant to accept the new PLM system. Donovan describes a situation he encountered at a Millipore plant in Puerto Rico. There, an engineer complained about not being able to find a long sought after schematic. He was not convinced the PLM system could help him. Using ProductCenter’s flexible search tools, Donovan quickly found the document based on the little bit of information the engineer knew about it. “When he saw the schematic, his face lit up. I had a convert right then.”
The Future:
Millipore plans to expand its use of ProductCenter to more closely integrate other corporate information technology, as well as to other groups, and perhaps later to its mechanical engineering subcontractors. They plan to shortly implement ProductCenter™ PLM Workflow to automate engineering change order processes and will later integrate ProductCenter to their Oracle® ERP system. This is expected to improve data consistency between the systems, which, in turn, will reduce scrap and rework for additional cost savings and time-to-market improvements.
Donovan concludes, “That’s Millipore’s vision for ProductCenter – to keep building on success.”