ProductCenter PLM Facilitates Global Operations at Saint-Gobain Crystals Division
Saint-Gobain Customers Say Controls Implemented with ProductCenter PLM More Impressive Than ISO Certified Plants
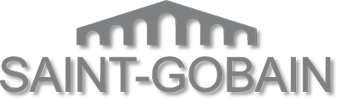
The Company:
As the world’s second oldest company, Saint-Gobain’s origins date back to the founding in France of Manufacture Royale des Glaces de Miroirs (Royal Mirror Glass Works) in 1665. Over the course of its development and diversification, Saint-Gobain has consistently been at the forefront of successive industrial revolutions, with technological innovations for the home and industry, a global workforce of over 175,000 and profitable operations topping $30 billion annually.
The Situation:
Saint-Gobain’s Crystals Division grows, cuts, and produces a broad range of crystals and detectors for diverse applications, including medical imaging, bone densitometry, and geophysical exploration. In the mid-90’s, the Crystals Division looked to upgrade the technical capabilities of its engineering organization, focusing specifically at newer computer-aided design (CAD) technologies and product lifecycle management (PLM) solutions.
The first order of business was to upgrade the group’s 2D CAD to 3D to take advantage of the enhanced visualization and relational capabilities that the technology offered. A scaled down version of Pro/Engineer® available at that time was selected. After that, the group, which relies heavily on modified standard designs and at that time was managing product data through paper processes, wanted a more efficient system, especially for managing this more complex 3D data, as well as for improving coordination among its global engineering and manufacturing.
The Solution:
Following an evaluation of available options, ProductCenter™ PLM, a PLM solution from SofTech, Inc., was chosen for its ability to integrate to Pro/Engineer. Scott Huth, director of engineering for the Scintillation business of the Crystals Division expands on the reason for their decision, “With all of the subcomponents and sub files required with Pro/Engineer, it would be very difficult with the number of modified standards that we produce to effectively manage all this data without ProductCenter. Also, other solutions we looked at weren’t what we would consider enterprise-wide and we needed the ability to tie in international operations.”
Today, over 100 employees from engineering, production, materials management, quality, customer service, and sales from plants in Nemours, France, and Newbury, Ohio, and Bangalore, India use ProductCenter. The group expects to continue to expand the use of workflow into the Bangalore, India operations in the very near future for engineering support, notifying them of modifications needed through a workflow process automated with ProductCenter™ PLM Workflow.
“At Newbury, ProductCenter and ProductCenter Workflow are used exclusively for managing all of our engineering documentation, revision control, engineering change processes, and quote processes that come through engineering, as well as our return process and new design release process to manufacturing. We have gone paperless on all of those.”
The flexibility of ProductCenter Workflow easily accommodates different nuances of the group’s design and release processes and support of their global operations. Engineering change notices (ECNs) are routed differently based on whether they are for a component or an assembly. Assembly ECNs get routed to production to notify them of an impending change and for early input. If the ECN is for a component, it gets routed through purchasing to notify them that they have an open work order and to forward a drawing to the supplier. “Now, everyone who needs to be is involved in decision making early on, fostering a much better spirit of cooperation,” adds Huth.
Before ProductCenter, it was common for people to work from drawings in their file cabinets that weren’t always current. Today, through use of the ProductCenter™ PLM Web Client, anyone authorized to do so can easily find and pull up a PDF (Adobe® Portable Document Format) of a current drawing at anytime, from anywhere.
“We’ve also revamped the way we document our assembly work instructions. Those are all in ProductCenter associated to the assembly print. It’s all there in ProductCenter, including engineering reports on experiments.”
The group’s India-based engineering support organization, which is involved on a major redocumentation effort, will soon be linked with ProductCenter Workflow for requests to make changes or start a new project; processes previously done via fax or email. ProductCenter’s ability to allow queries on workflows and extended reporting capabilities makes it easy to track workflow progress anywhere in the world. Email notification is also used extensively to notify the next person in line of a task awaiting them, while the ProductCenter Web Client simplifies software upgrades, regardless of where the employee is located.
The group uses a non-confidential form of a design drawing called a sales drawing to provide to customers and prospects. Design drawings and sales drawing are linked to the same model in ProductCenter. If one is changed, the other is automatically updated. Linking the two in ProductCenter ensures that information relayed to customers and prospects is always accurate and up to date, as well as fully documented for later manufacture.
In addition to centralizing product data and improving design through manufacturing efficiency, ProductCenter has also impacted the bottom line. “Being able to access and distribute PDFs of sales drawings to customers, production, and purchasing has improved our customer responsiveness. By using workflow routings based on the level of complexity of the request, we have decreased our quote cycle times on engineered quotations by roughly 20% over the past two years.”
In summary on the benefits derived through use of ProductCenter Huth is quick to point out, “We’re not ISO certified, but in customer audits, after they see what we’ve accomplished with ProductCenter, customers often comment that what we’ve done is well and above what they usually see in an ISO certified plant. They have been impressed with that.”