ProductCenter® PLM at Haydon Kerk Motion Solutions
ProductCenter PLM Reduces Design Cycle Times and Cost by Streamlining Data Management and Business Processes
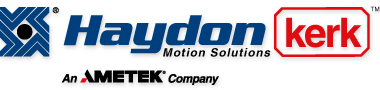
About Haydon Kerk Motion Solutions:
Haydon Kerk Motion Solutions is a unit of AMETEK, Inc., a leading global manufacturer of electronic instruments and electromechanical devices with annualized sales of $3.0 billion. Haydon Kerk Motion Solutions is the joining of two world-class brands in the field of linear motion; Haydon Switch and Instrument, Inc. and Kerk Motion Products, Inc. Together as Haydon Kerk Motion Solutions, it offers a wide range of high-performance and precision linear motion products.
Recognized as a leading manufacturer of stepper motor-based linear actuators, rotary motors, lead screw assemblies, and linear rail and guide systems used in niche market applications, Haydon Kerk Motion Solutions has developed industry-renowned brands built upon its technical innovation, versatility, customization, product durability, and dedicated customer service.
The Situation:
In 2003, Haydon Kerk of Waterbury, Connecticut realized it needed to improve its product development and manufacturing practices due to the deficiencies of managing change processes and SolidWorks® design documents without a data management solution.
Haydon Kerk had a team of four to five employees dedicated to retrieving “paper” drawing files and ensuring that product development and manufacturing had the current version of the required drawings. Haydon Kerk’s vision was to utilize PDF files for viewing and sharing files throughout the organization, essentially making information available to any end user at any time and at any location.
The primary decision makers had prior experience with product lifecycle management (PLM). They knew they needed a solution that would allow Haydon Kerk to design and quickly implement workflows to manage and automate their Engineering Change Order (ECO) process. They needed a solution that they could deploy rapidly at its Connecticut operations and eventually expand to support the company’s global operations in the United States, Europe and Asia. Haydon Kerk recognized that utilizing one solution for its development and manufacturing processes, in all of its global locations, would bring tremendous cost savings and productivity benefits across all of its businesses.
The Solution:
Streamlining Business Processes, Reducing Cost
SofTech’s ProductCenter® PLM solution was selected for several key reasons including its proven history of fast implementations; flexible process automation that could adapt to Haydon Kerk’s business process requirements; and its ability to manage SolidWorks product design data. Additionally, automating the generation of PDF “viewables” through ProductCenter’s GenView product provided secure access to current product data to those involved in the product lifecycle process outside of engineering, including production personnel and quality assurance.
“We chose ProductCenter because it offered all the capabilities we needed out of the box, without heavy, costly customization,” states Gary Charlton, Haydon Kerk’s Director of Information Technology. “By streamlining our engineering change processes, enhancing collaboration, and improving control of our SolidWorks product data, we have achieved significant reductions in design cycle times and cost with ProductCenter, which in turn, benefits our customers.”
Expanding Usage, Enhancing Collaboration
After the initial implementation in Connecticut, Haydon Kerk expanded ProductCenter’s usage to facilitate the exchange of SolidWorks product information with its design center in China. New product designs for U.S. and European customers occur at the company’s U.S. operations. Alternatively, China primarily works on designs for the company’s China-based customers.
“ProductCenter has allowed for collaboration between our design centers in the United States and China in that our U.S. operations initiate designs and review the work that our China operations complete and when approved move the work forward,” explains Gary Charlton. “Bringing our design center in China into the product development process has definitely been an advantage to the business.”
The ProductCenter expansion continued with users at the Kerk Motion Products of Hollis, New Hampshire facility. “The Kerk users were open to change and welcomed the use of ProductCenter to improve their processes and gain efficiencies. ProductCenter has helped integrate the engineering groups of both companies, allowing us to become one virtual engineering group,” adds Gary Charlton.
Sharing Information, Increasing Efficiency
Today, Haydon Kerk utilizes ProductCenter throughout the entire organization with nearly one hundred users from Engineering, Quality, Manufacturing, Customer Service, Accounting, Finance and Purchasing. ProductCenter has expanded to become the corporate file archive for storing additional types of data such as packing slips as well as data needed to communicate with other groups within the organization. Furthermore, all shipment information for each day is scanned and filed into ProductCenter.
For the casual users who access ProductCenter far less than the Engineering group, Haydon Kerk utilizes an intelligent ProductCenter client for finding and adding information. With little training, users are able to drag and drop a file into a window, enter appropriate attributes and edit the file in other ways as required and authorized. Haydon Kerk is looking to expand on these tailored clients for specific departments.
The manufacturing floor utilizes a Find, View and Print client, which gives users the ability to enter a part number, then view and print the PDF file they are searching for. These simple configurable clients allow Haydon Kerk to even further simplify the ProductCenter user experience and expand its usage throughout the company.
When asked about the benefits Haydon Kerk has achieved since implementing ProductCenter Gary Charlton explains, “Before ProductCenter, our processes were paper based. Now ProductCenter gives us the ability to move data between and among departments and throughout our company more efficiently. It is not just about getting all of the information out to everyone. It is about getting the right information to the right people when they need it. We have increased our productivity as the information is at our fingertips.” “By automating our ECO process and improving the management of our design data, we have been able to reduce our costs in terms of time savings and design re-use,” adds Gary Charlton.
Supporting Standards
Haydon Kerk also utilizes ProductCenter to support its International Organization for Standardization (ISO) certification and International Traffic in Arms Regulations (ITAR) requirements. “ProductCenter has helped streamline our ISO process. The ISO auditors recognize the control that we have over our product information with ProductCenter, which makes the certification process straightforward,” explains Gary Charlton. “We also use ProductCenter’s classification capabilities to segregate our ITAR information and limit access to only those allowed personnel through the permission model, which makes it easy to ensure that any documents or drawings restricted by ITAR are not shared with our overseas operations.”
The Future:
Haydon Kerk is looking to add additional data and processes covering the full life cycle of a product and making all of that information available via a simple search in ProductCenter. Additionally, ProductCenter’s user base will continually expand throughout Haydon Kerk. ProductCenter’s configurable clients will enable each specific department to fulfill its own set of requirements for efficiently accessing and adding information.
“ProductCenter works very well for Haydon Kerk and doesn’t require a lot of support. Compared to other software products ProductCenter’s customer support team, stability and ease of use rank it at the top,” states Gary Charlton. “We are continually looking at expanding ProductCenter’s capabilities to improve our product development efficiency in order to stay competitive and meet the challenges of today’s evolving global marketplace.”