ELCAN Optical Has Clear Vision for PLM
SofTech’s CAD integrations become a significant part ELCAN’s PLM solution strategy
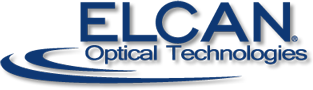
The Company:
ELCAN Optical Technologies is a leading provider of precision optical and electronic solutions for defense, medical, industrial, commercial and entertainment markets. A Raytheon company, with over 1100 employees in Canada, Spain, and the U.S., ELCAN enjoys a premier reputation in optics. Its history spans 157 years from its earliest work with Leica camera lenses and major cinematography achievements, such as the Panavision lenses and 70mm IMAX projection systems. ELCAN’s success continues today, with state-of-the-art sport and military rifle sighting systems, medical optical systems, digital displays, and many other state-of-the-art optical advancements.
The Situation:
During an Executive Leadership Workshop a few years back, ELCAN’s rapid growth was identified as a ‘burning platform’; one that could burn out of control if not managed properly. Growth was obviously a good problem to have but ELCAN had the forethought to know it needed to manage it right, especially without adding staff.
Dedicated to continuous improvement and using techniques from the Raytheon Six Sigma™ approach, ELCAN followed a six step process to guide it through an assessment of its current business processes and to put into operation improvements that would support growth.
Attendees brainstormed, visualizing the future and how ELCAN would function with improvements in these areas. One of the first areas targeted was the Configuration Management Office (CMO). Resources were assembled to document existing CM processes in detail. “We ‘stapled’ ourselves to every CM process, identifying duplicate or undue efforts, how each piece of paper was handled, signed off, and moved throughout the organization,” explains Gunter Schmidt, ELCAN Manager of Product Quality. “It was a very revealing undertaking.”
The group uncovered excessively high queue times in CM, too many signatures, steps, replicated tasks in different software, checking and rechecking of each other’s work, and undue logging, stamping, and copying of documents. The bottom line: the CMO suffered from too much bureaucracy, adding cycle time, costs, and errors that jeopardized not only growth but also customer satisfaction.
“Once we had our hands around the problem and new processes defined, we benchmarked PDM/PLM solutions to help us automate new, leaner workflows, with the ultimate goal to reduce release cycles and costs by 50%,” adds Schmidt. This led to the eventual implementation of a solution. However, shortly thereafter, the software provider dropped support for AutoCAD, ELCAN’s primary design application, and then the PDM software completely, leaving the company in a lurch.
The Solution:
It was back to the drawing board for ELCAN with a whole new PLM evaluation. After a rigorous review, ELCAN narrowed the companies down, eventually selecting SofTech, Inc. as its PLM solution provider.
Three things stood out that gave ELCAN confidence about SofTech and its ProductCenter™ PLM solution. First, Elcan didn’t want to get stuck again without support for its primary CAD tool. SofTech offered a wide spectrum of direct ProductCenter integrations to popular CAD solutions, including AutoCAD, as well as Autodesk Inventor, Mechanical Desktop, Pro/Engineer, SolidWorks, and others. This made it especially useful for mixed-CAD environments, whether inherent within a company or for collaborating with customers, suppliers, or partners like ELCAN.
It was unlikely support for these applications would go away. SofTech’s CAD integrations are in fact a significant part of its PLM solution strategy and history. As early as 1992, SofTech was one of the first to support the newer, more complex 3D modeling applications, such as Pro/Engineer, then uncharted territory for independent data management solution providers. SofTech today is also a long-standing partner in the Autodesk Certified Application Program, and other partner programs with SolidWorks and PTC, ensuring high quality compatibility release to release.
The second factor was ProductCenter’s low cost of ownership. “ProductCenter was cost competitive, with a flexible licensing model, and required minimal admin support,” adds Schmidt. “ProductCenter’s flexible data modeling and workflow also let us mold ProductCenter to our business, without compromise, so we didn’t need a lot of programmers and expense to make this happen. It also supported more stringent data access and security controls in compliance with International Trade and Arms Regulations (ITAR), critical to us as a military supplier.”
The third factor influencing ELCAN’s selection was SofTech’s personnel; their knowledge and dedication. SofTech stood out with a solid history of customer success and extremely quick implementations. “SofTech personnel worked very closely with us during a pilot of ProductCenter to prove it in our environment beforehand, minimizing our risk,” Schmidt relays. “Once the final decision was made to go with SofTech, we were in business in eight weeks, with all existing product data migrated to ProductCenter and workflows automated.”
A few years have passed since that first workshop and the results have been impressive. Over 175 ELCAN employees are now on ProductCenter. There’s no more microfilming and excessive copying of documents. ECR/ECOs and other document reviews and distribution are completely automated. Data is accurate and consistent. Customers are satisfied. Cycle times and costs are down 50 percent or more. With PLM now just part of everyday operations, ELCAN has saved over a million dollars.
The Future:
ProductCenter has stepped right in and shown its capability to contribute to ELCAN’s future success. As with the Raytheon Six Sigma™ approach, it’s time to celebrate achievements, while building for tomorrow. Plans are underway to apply ProductCenter PLM to automate other areas of ELCAN’s business, including ELCAN’s contract review and approval process, supplier inspection reports and rejects, as well as corrective actions. There’s more to be done.