Cryogenic Industries Gels with SofTech’s ProductCenter PLM
As the Global Business Solution, ProductCenter PLM Connects Cryogenic Industries Contributing to the Company’s Industry Leadership Position
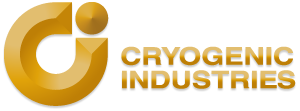
About Cryogenic Industries:
Cryogenic Industries (CI) is comprised of several affiliated companies, including ACD, Cosmodyne, Cryoquip and Rhine Engineering that engineer, manufacture and service equipment for the industrial gas, petrochemical and new energy industries worldwide.
Headquartered in Murrieta, California, CI leads the industry in cryogenic gas handling, transporting and process equipment. CI’s products range from air separation units, LNG (liquefied natural gas) liquefiers, vaporizers, heat exchangers and food freezers to cryogenic liquid samplers, reciprocating and centrifugal pumps, and turbo-expanders.
CI has manufacturing facilities, technical support personnel, and service and repair centers strategically located around the globe to fulfill the company’s commitment to continually provide quality products and services to its customers.
The Situation:
Cryogenic Industries had been managing its product data with shared network folders where various drives were utilized to store data and rights were granted according to business unit. There were many costly disadvantages to this data management structure in terms of time, productivity, collaboration and lack of controls.
Upon recognition of how these practices were impeding the progress of the business as a whole, support for a Product Lifecycle Management (PLM) solution search took shape. Cryogenic Industries needed a system that could integrate with its diverse CAD applications to control the company’s Intellectual Property (IP) through its product engineering drawings and streamline collaboration across all of its businesses.
The Solution – Informed Decision Making:
After several demonstrations from various PLM vendors were completed, Cryogenic Industries decided to take advantage of the ProductCenter® PLM Pilot Program. This is a low-cost, low-risk process for the high-risk undertaking of a PLM implementation and a practice that differentiated SofTech from other vendors.
The ProductCenter PLM Pilot Program was structured so that SofTech spent one week at the ACD facility where the PLM server would reside and while on site, set up a ProductCenter environment using ACD’s product design data. During the interactive sessions, SofTech demonstrated ProductCenter’s capabilities providing users with the knowledge and tools to then evaluate the application. Users were able to perform tasks related to their job responsibilities such as vaulting and managing CAD design data and benefited by gaining visibility of the data throughout the organization by automating processes, such as drawing approval through workflow.
Proof is in the ProductCenter Pilot Program:
“The ProductCenter Pilot Program answered our questions and provided valuable insight into the implementation cost, efficiencies to be gained, user training and learning curves, future opportunities for the PLM system as well as the expected impact on our corporate culture. SofTech worked with us and extended the program for 3 months so that we could grasp a clear understanding as to the global concept of PLM use,” states Ted Pardo Jr., Director Global Information Technology and ProductCenter Project Lead for Cryogenic Industries.
“Upon successfully completing the pilot, ProductCenter PLM was selected because of SofTech’s support and cooperation as well as the performance and flexibility of the application,” adds Pardo. “The Pilot program enabled us to prove that ProductCenter was the right solution for Cryogenic Industries and was also beneficial as it jumpstarted our implementation and minimized the impact to the users as they were already familiar with the application.”
One of the key factors in CI’s selection of ProductCenter was its ability to accommodate a mixed CAD environment, facilitating management of the SolidWorks®, Autodesk® Inventor®, AutoCAD® Mechanical and AutoCAD® Electrical product design data of the different business units.
Streamlining Global Data Access & Enhancing Collaboration:
The ProductCenter implementation began with loading the production engineering data of ACD, Cosmodyne and Cryoquip into a centralized database followed by user training. CI implemented a classification structure and permission model designed to separate product information of the different business divisions providing secure, controlled access.
“ProductCenter was implemented to control Cryogenic Industries’ intellectual property (IP) which is documented through our product engineering drawings. ProductCenter has allowed us to guarantee the accuracy, reliability and availability of our IP in a way that we had not experienced before. One might say that if it’s not in ProductCenter then we don’t need it,” explains Pardo.
The implementation quickly expanded to incorporate the company’s overseas engineering design and manufacturing services into the product development process initially with Rhine Engineering based in India. Rhine Engineering retrieves released drawings generated by CI’s designers and then manufactures products for customers in India. ProductCenter provided immediate results with improved product data management, and streamlined global data access and collaboration across the Cryogenic Industries enterprise.
Supporting Compliance Standards:
Cryogenic Industries has extended ProductCenter’s use past engineering to control critical business documents for supporting compliance standards such as the American Society of Mechanical Engineers (ASME), European Pressure Equipment Directive (PED), Special Equipment Licensing Office (SELO) in China and Korean Gas Safety (KGS). “We have increased the scope of the ProductCenter implementation to securely manage not just engineering data but also business documents related to the manufacturing and designing of our products,” states Pardo.
An example of supporting standards is at the Cryoquip facility where ProductCenter manages all of the business documents related to the manufacturing of its pressure vessels governed by the ASME and PED. All documents that come in with controlled materials are signed off, stamped and checked into ProductCenter. “In the event of an audit, Cryogenic Industries has to be able to present documentation that shows we have followed the specific procedures required to meet compliance standards. Having this information electronically controlled and available in ProductCenter provides us with the traceability we need to conform to the different compliance standards of our businesses,” explains Pardo.
Improving Efficiency, Connecting Business Divisions:
ProductCenter has allowed CI to successfully expand Cryogenic Design Services (CDS) also located in India, a group which provides engineering services for CI’s growing businesses. The CDS resources, proficient in AutoCAD and SolidWorks, are able to access ProductCenter to complete design changes by modifying drawings that meet specifications as directed by ACD, Cryoquip and Cosmodyne.
ProductCenter’s replication management strategy controls what data is released to CDS India. The replication feature pushes information out to the CDS group�s remote local vault where the files are then retrieved, modified and returned back into the vault located at ACD in California. ACD also has a local vault in Germany. As users in Germany change or complete a drawing, they move the drawing into the In-Approval status and the engineering manager at ACD reviews and releases accordingly.
Additionally, ProductCenter has brought CI’s companies together. As an example, Cryoquip manufactures Cosmodyne’s products. Through ProductCenter, Cryoquip has access to Cosmodynes latest released drawings and also has the ability to print released drawings on the shop floor for production. Having the design data immediately available and easily accessible improves the release to manufacturing process.
Enterprise Integration & Positive Returns:
ProductCenter also has been integrated with CI’s ARev and Epicor® ManFact ERP systems to enable the bi-directional exchange of product information and eliminate re-keying of data. In addition, when new Bills of Materials (BOMs) within the ERP system are to be released, checks are performed verifying that what is being released is in accordance with the latest version and revision in ProductCenter.
“We have seen positive returns from ProductCenter’s integration with our ERP system and expect that the communication between our PLM and ERP systems will further improve our efficiency and processes,” Pardo adds.
Increasing Productivity with Time Savers SolidWorks Toolbox & Design Library:
As a world leading manufacturer of cryogenic pumps and turbo-expanders, ACD is continually looking at strategic ways to improve its business practices in order to meet the challenges of today’s evolving global marketplace. Since the implementation began, ACD’s product design environment changed with ProductCenter facilitating the transition to SolidWorks as ACD’s primary CAD tool.
When asked about the strengths of ProductCenter and SofTech, Ted Pardo Jr. states “The responsiveness of SofTech listening to our needs and working with us as ACD transitioned to utilize SolidWorks as its primary design tool was a testament to SofTech’s commitment to our success with ProductCenter and has strengthened our partnership.”
ProductCenter’s long-time status as a SolidWorks Certified Gold Partner Product and tight integration with SolidWorks enables ProductCenter to manage the complete design, including Toolbox and Design Library parts.
Since the migration to SolidWorks, ACD has increased its productivity by utilizing the SolidWorks Design Library feature with ProductCenter as a central location to store items regularly used such as components, parts, assemblies and drawings. ACD also utilizes the SolidWorks Toolbox feature with ProductCenter, providing users with immediate access to the latest collection of standard components, predefined by ACD to use in its designs, such as screws, bearings, washers, fasteners and nuts.
“Using the SolidWorks Toolbox and Design Library features with ProductCenter saves us time and increases our output. Having the ability to drag and drop standard components into our designs allows us to improve our global engineering efforts through tracking, quality and maintainability,” explains Pardo.
The Future of ProductCenter at Cryogenic Industries:
Cryogenic Industries intends to further improve business operations and processes by utilizing ProductCenter to manage agreements and legal documents tied to specific customer projects.
CI also will evolve its current BOM management process with ProductCenter, especially at companies such as Cosmodyne, an established manufacturer of cryogenic air separation plants and liquefiers, which deals with very large and complex BOMs.
Ted Pardo Jr. adds, “We are looking to ProductCenter to increase visibility, accessibility and security. Cryogenic Industries views ProductCenter not just as an Engineering solution but as a global business solution that proves to be a tremendous benefit to our company’s success.”